We continue on our epic learning journey with Taylor’s Master Guitar Designer, Andy Powers, as we dive into topics like sustainability, changing music trends and how Taylor selects their woods for guitars.
This was a part of our live virtual Q&A session with Andy Powers a while back, which we hosted for a number of lucky participants. Andy answered a host of great questions from the participants and we just had to share them with everyone.
If you’ve not read part 1 of our live session with Andy Powers, make sure you read it here!
As a buyer and guitar enthusiast, we favour supporting a company with strong ESG (environmental, social and corporate governance) values. What is Taylor’s view on the future of guitars in terms of sustainable wood sources and fair trade practices? Most recently, has COVID-19 impacted this strategy?
As far as our environmental and sustainability practice goes, it’s never been a destination, more of a journey and how you get there. For us, every one of those choices is an action. There isn’t a list of specifications that we can check off and say, “hey, now we’re sustainable and carbon neutral!” it’s more of a mindset.
In everything that we do, we keep in mind the impact our work has. The way Bob Taylor would describe it – he doesn’t want anything or anybody to suffer in order to own or play that guitar. Now that goes from somebody who’s working in a village in a remote place who’s cutting wood, or someone who’s working in our factory building the guitar, or someone whose job is to transport or distribute wood – we want everybody and anything along that chain to be participating in the most healthy and sustainable way possible. What that means is that as time develops and as much as we’re able to, we want to be planting trees deliberately because we want to leave forests in a better condition than when we first found them. So that means, if you cut a piece of wood down – use THE WHOLE THING. Don’t eat the heart and throw away the rind – you want to find out how to make every bit of that wood count. And it also means looking for alternative sources.
We’ve recently launched a series of guitars where we use what we call “Urban Woods”. These are trees that are planted on purpose for shade value, wind breaks, noise barriers, aesthetic value, or any other reason throughout cities. A number of years ago we started looking back and wondered: why not those trees? What happens to those trees when they become too large and have to be removed because they become a hazard to the people around them? When we started looking at the trees throughout Southern California, we found out some of them are first grade guitar making woods. So we started to incorporate urban-sourced trees into our guitars, tapping into that as a resource.
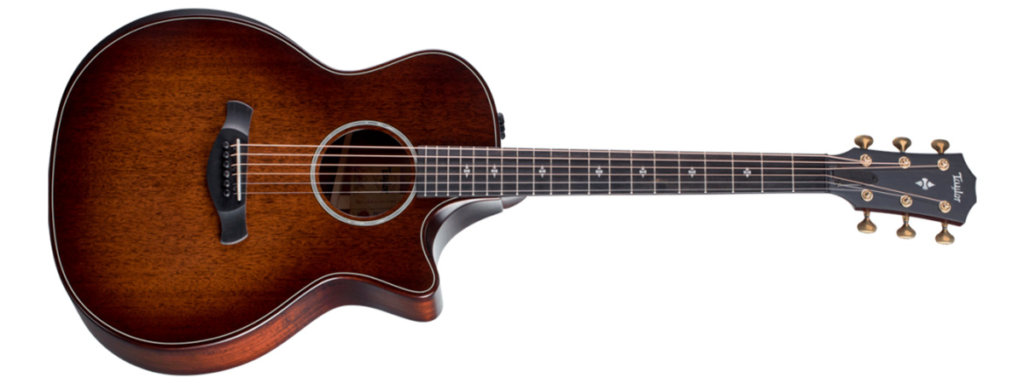
We’re also looking at repopulating entire forests in Hawaii and Africa. A lot of those projects are what I’d call forward thinking, but we know that they need to be done, even when it comes to the design of the guitar itself. You’re going to have to design things in a way that makes efficient use of material, use healthy, ecologically sound materials, and you’re gonna distribute them in healthy ways too. So for us throughout our factories, forestries, and throughout our guitar making, the process towards becoming more sustainable is just that – it’s a process. That’s something that we’ve been committed to, and will be more and more as we go on, because that’s the world that we live in. We of course still want to be using wood for guitars and that’s why we need to do it in a responsible way.
What’s more sustainable than an instrument that can be played for the next hundred years or more?
A lot of times people will ask us why we don’t make a guitar made from plastic, or some synthetic materials. There’s a whole bunch of technical reasons why I like wood, but if you look at what goes into building man-made synthetic materials – whether it be plastic, carbon fibers, carbon composites – you’ll learn that most of those materials are more environmentally damaging than wood. So when you look at almost any other consumer good, maybe the toys for your kids or furniture for your house, you look at wood and you think that is a natural, ecological sound material.
In the process of growing that tree, you’re providing habitats for wildlife, you’re providing carbon sequestration, you’re providing all kinds of amazing environmental benefits. And then, at the end of that tree’s life, you get a super long lasting and heirloom piece – that’s a super sustainable thing! What’s more sustainable than an instrument that can be played for the next hundred years or more? I think that’s amazing and that’s something we’re deeply committed to, even in this pandemic. In the future, for the rest of our working life times, this is a value to us that we’re not going to give up.
Where does Taylor see themselves as contributors to the acoustic guitar player and acoustic music, as we see more and more music shifting into the electronic scene?
I can tell that in the thousands of years that people have been playing music, I don’t see that going away. As long as there are people, and there are stories to be told, people are still going to be playing instruments. And the acoustic guitar has turned into this universally appealing instrument, because it’s portable, harmonic, rhythmic, melodic, accessible and readily adaptable to almost every musical style. Because of that, it’s a historically important instrument.
As a builder, I have an interest in making instruments that serve any group of musicians. As those needs change, and as players invent new styles and are asking more of their instruments, I want to be able to respond to that. If they’re looking for more dynamic range, I want to be able to build a guitar with more dynamic range. If they need an extended harmonic vocabulary, or more volume, I want to improve those designs as we learn more and do a better job of building the instrument. I want to build an instrument that is more than what a musician could ask for.
While Leo Fender never had Jimi Hendrix in mind while designing the Stratocaster, aren’t we glad that he did what he did! So as a builder, that is the sort of mindset that I want to bring to these instruments, so that the musician is constantly finding fresh inspiration to make new creative music.
That’s the way I see instruments and the makers over time when I look at it historically. Going back 50, 100, 200 years, it’s what I’d describe as a two way street – musicians might ask for some unique quality that they might not have on their existing instruments, and it’s the makers job to respond. And if the maker is doing their utmost job to build great instruments, they’re going to build something that’s more than what a musician would ask for. That inspires the musician to take on a new musical style, take on a new technique and sound.
An easy example – when Leo Fender was designing the Stratocaster, he was thinking of western swing music like Bob Wills and some of the contemporary country music that was being played in Southern California back in the 50s. Maybe even the rockabilly music you’d hear from Gene Vincent and the Blue Caps and some of those bands. And yet, the things that he put into that guitar allowed Jimi Hendrix to take that instrument and make all kinds of crazy sounds and really expand what the guitar could mean in modern, contemporary, popular music! While Leo Fender never had Jimi Hendrix in mind while designing the Stratocaster, aren’t we glad that he did what he did! As a builder, that is the sort of mindset that I want to bring to these instruments, so that the musician is constantly finding fresh inspiration to make new creative music.
Every piece of wood is different, even if they’re the same species of wood, how do you determine that a certain piece of wood has a satisfactory tonality before you start building the guitar?
When I look at different pieces of wood, I’m reminded of something an old furniture maker friend taught me when I was younger. He told me that a good craftsman will be able to take a piece of wood and turn it into anything they want. But a great craftsman will ask the piece of wood what it naturally wants to be and allow it to do that. Because that’s what the piece of wood really wants. If you’re selecting your material appropriately, you want to take the right piece and type of wood and turn it into the part you wish to make, because that’s where it’ll reach its highest form of functioning.
A good craftsman will be able to take a piece of wood and turn it into anything they want. But a great craftsman will ask the piece of wood what it naturally wants to be and allow it to do that.
When we look at these different woods – whether it’s East Indian rosewood for the back and the sides, walnut or maple or mahogany or spruce for the top – largely those woods will behave like each other. For example, walnut tends to have a certain amount of uniformity among that species. For certain parts, I wouldn’t use that wood because even if I could use it for something, it’s probably not as effective or efficient for that one part. I could choose East Indian rosewood for that part, or maybe if i’m looking for an efficient, bold sounding top, I’m not going to choose a piece of curly maple to build the top of a guitar. That will tend to level out the response because that maple is somewhat hard and more dense and heavy, making it almost like a natural compressor.
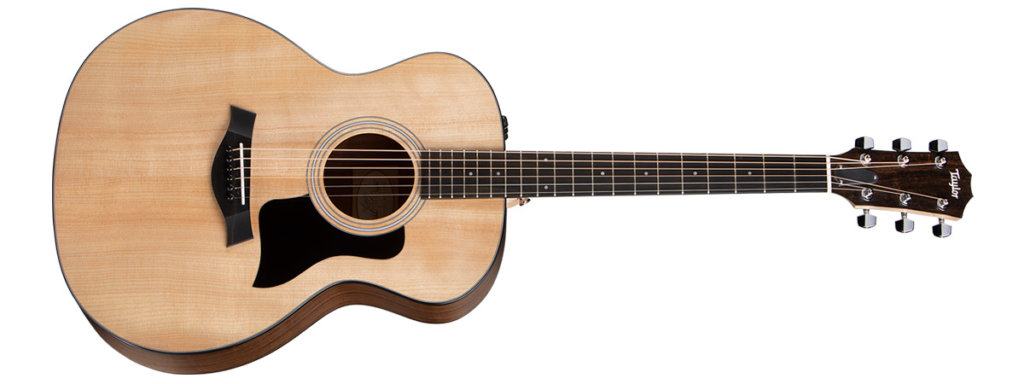
To begin with, you want to choose the right types of wood for the right parts you’re building. Past that, you can start to grade those materials into a specific set of guidelines. You can look at things like the weight, the density and even more technical terms which will get hard to explain! One of those technical terms is the velocity that sound travels through the piece of wood at – that’s one of the criteria that I look at. You can also look at bending and stiffness and deflection, the mechanical impedance – for a certain amount of energy that is input, how much is absorbed – certain woods will be very absorbent and they act almost like a vibration absorber rather than allowing that vibration to propagate through that piece of wood.
There are lots of different attributes that you can test, and the way that most guitar makers will evaluate those is through an experiential approach. When you see somebody tap on a piece of wood, and they tap on wood every day for thirty years, they get a pretty good sense of how that piece of wood is going to respond. I’ve done a lot of that, but I like to mix it with some additional data points when I’m able to because that helps complete your knowledge and fill it out. I’ve done things like fast Fourier transform (FFT) spectrum analysis and more scientific-minded tests on woods.
We want to build great guitars on purpose, not by accident…
For us in a production setting, we tend to rely a lot on sorting. Let’s say we get a load of a thousand sitka spruce tops, I’ll look at those thousand tops and see that based on weight, they’ll fall into these three categories – these ones will be very stiff, harder and a little heavier, these will be in the middle range, these ones will be much lower stiffness and weight, or a mix of those. You can shuffle them towards different designs that were optimised to handle wood that fell within a certain set of parameters, rather than using one top that was really too heavy and stiff on a design that was meant to be a real lightweight top – that’s not going to be a great guitar. We want to build great guitars on purpose, not by accident, that’s why we do things like sorting woods for their optimal characteristics for certain designs.
There’s still more to come! Watch this space if you can’t get enough of learning from Andy Powers – we’ll be diving into acoustic guitar “perfection”, his advice on buying an acoustic guitar and why they improve with age.